Page 1 of 4
Torque arm bolt
Posted: Tue Oct 14, 2014 6:07 pm
by 1200boxer
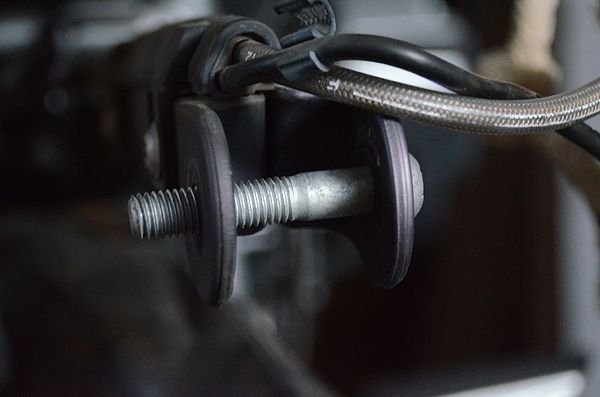
This is my torque arm bolt.The plain shank reaches less than half the length between the holes which makes the threads bear on the arm wall.It doesn't seem to be very good practice to me.Should I replace it with a bolt wiith a shank that spans the entire width?
Posted: Wed Oct 15, 2014 2:36 pm
by Droptarotter
Is that the stock bolt? It's been awhile since I had mine apart and can't remember if the unthreaded portion is longer. The parts fiche is no help either.
It does make sense to have a longer unthreaded portion on that bolt.
Not much help, eh??
Cheers
Posted: Wed Oct 15, 2014 4:57 pm
by 1200boxer
I'm pretty sure this is factory fitted.I've looked at the parts diagram and there's no detail on the bolt.Will an off the shelf galvanized allen headed bolt do?
Posted: Thu Oct 16, 2014 4:17 pm
by Droptarotter
Yes!
Cheers
Posted: Thu Oct 16, 2014 6:13 pm
by Boxadog 2000
1200boxer wrote:I'm pretty sure this is factory fitted.I've looked at the parts diagram and there's no detail on the bolt.Will an off the shelf galvanized allen headed bolt do?
MOST DEFINITELY NOT
Firstly you probably wont find a Galvanized cap head screw, zinc plated maybe.
If you do find one you must be 101% sure that it has been de embritled.
Why because when a bolt is plated, you guessed it they become brittle and can lose over 50% of there tensile strength
Posted: Sat Oct 25, 2014 4:26 pm
by Tapio
Late anwer, sorry.
The thread length doesn't matter at all.
See my crappy paint sketch. Facebook changed their programmng code, so i don't know how to to upload pics, but here it is:
https://scontent-b-ams.xx.fbcdn.net/hph ... e=54EEE9BA
It shows two steel bars held together by the blue fastener. There's a force F that pulls them apart. Now, if the fastener is a rivet, the force would be transmitted through the rivet at the two vertical red lines.
If the fastener is a screw and nut, the bars are forced together at the green horisontal lines. The force in this case is transmitted via the bar surfaces, at the yellow horisontal line. The screw does not take part in transmitting the force at all.
I hope this makes sense to you.
@Boxadog 2000: i'm by no means an expert on this, but as I understand it, zinc plating is done by placing an anode and a kathode in a liquid containing an electrolyte of some sort. You put an electrical current to the anode and kathode. The anode is zinc and the kathode is the thing you want to plate. I cannot see how this could make a steel thingy become brittle.
//T
Posted: Sat Oct 25, 2014 4:40 pm
by Blackal
Tapio wrote:Late anwer, sorry.
The thread length doesn't matter at all.
See my crappy paint sketch. Facebook changed their programmng code, so i don't know how to to upload pics, but here it is:
https://scontent-b-ams.xx.fbcdn.net/hph ... e=54EEE9BA
It shows two steel bars held together by the blue fastener. There's a force F that pulls them apart. Now, if the fastener is a rivet, the force would be transmitted through the rivet at the two vertical red lines.
If the fastener is a screw and nut, the bars are forced together at the green horisontal lines. The force in this case is transmitted via the bar surfaces, at the yellow horisontal line. The screw does not take part in transmitting the force at all.
I hope this makes sense to you.
@Boxadog 2000: i'm by no means an expert on this, but as I understand it, zinc plating is done by placing an anode and a kathode in a liquid containing an electrolyte of some sort. You put an electrical current to the anode and kathode. The anode is zinc and the kathode is the thing you want to plate. I cannot see how this could make a steel thingy become brittle.
//T
Zinc plating is also done by the cheaper method of Hot Zinc Dipping. This is almost universal when it comes to pipe spools etc, where the electrolyte bath would prove dificult. Hot Zinc Dipping also puts a thicker lair of zinc, to allow for wastage by erosion.
Al
Posted: Sat Oct 25, 2014 6:09 pm
by boxerscott
what bike are we talking about?

Posted: Sat Oct 25, 2014 6:37 pm
by Droptarotter
Just use a stainless bolt. I have two aftermarket torque arms on my bikes and they both came with stainless bolts.
One was a Verholen, sp??, and can't remember what is on the 12S at the moment.
Cheers
Posted: Sat Oct 25, 2014 9:11 pm
by Corvus
Tapio wrote:Late anwer, sorry.
The thread length doesn't matter at all.
See my crappy paint sketch. Facebook changed their programmng code, so i don't know how to to upload pics, but here it is:
https://scontent-b-ams.xx.fbcdn.net/hph ... e=54EEE9BA
It shows two steel bars held together by the blue fastener. There's a force F that pulls them apart. Now, if the fastener is a rivet, the force would be transmitted through the rivet at the two vertical red lines.
If the fastener is a screw and nut, the bars are forced together at the green horisontal lines. The force in this case is transmitted via the bar surfaces, at the yellow horisontal line. The screw does not take part in transmitting the force at all.
I hope this makes sense to you.
@Boxadog 2000: i'm by no means an expert on this, but as I understand it, zinc plating is done by placing an anode and a kathode in a liquid containing an electrolyte of some sort. You put an electrical current to the anode and kathode. The anode is zinc and the kathode is the thing you want to plate. I cannot see how this could make a steel thingy become brittle.
//T
It's a while since I was involved in this kind of thing, but my understanding is that the process involving zinc plating can induce hydrogen embrittlement. The process should be followed by passivation, if my memory serves correctly (Relying on memory is risky!)
http://en.m.wikipedia.org/wiki/Hydrogen_embrittlement
I agree with with Boxer dog. I've seen, first hand, examples of bolts fail easily under tension because of hydrogen embrittlement.
Edit: another associated link
http://www.heat.com.au/treatments-de-embrittle.php
Posted: Sat Oct 25, 2014 9:23 pm
by Corvus
Tapio wrote:Late anwer, sorry.
The thread length doesn't matter at all.
See my crappy paint sketch. Facebook changed their programmng code, so i don't know how to to upload pics, but here it is:
https://scontent-b-ams.xx.fbcdn.net/hph ... e=54EEE9BA
It shows two steel bars held together by the blue fastener. There's a force F that pulls them apart. Now, if the fastener is a rivet, the force would be transmitted through the rivet at the two vertical red lines.
If the fastener is a screw and nut, the bars are forced together at the green horisontal lines. The force in this case is transmitted via the bar surfaces, at the yellow horisontal line. The screw does not take part in transmitting the force at all.
I hope this makes sense to you.
@Boxadog 2000: i'm by no means an expert on this, but as I understand it, zinc plating is done by placing an anode and a kathode in a liquid containing an electrolyte of some sort. You put an electrical current to the anode and kathode. The anode is zinc and the kathode is the thing you want to plate. I cannot see how this could make a steel thingy become brittle.
//T
I would agree that friction under the head of a bolt/nut would be intended to resist the load placed upon it, without relying on shear stress directly, as a pin would. This is where the grade of bolt is important, in allowing you to torque the bolt up sufficiently to induce the friction between surfaces without stretching the bolt beyond it's elastic limit(or it literally snapping as a result of hydrogen embrittlement).
Edit: I agree that the threaded portion doesn't matter "theoretically" provided friction alone is sufficient. But imagine if the bolt was, say, 10mm dia and the hole was , say, 12mm dia. Even if the bolt was strong enough to induce friction, would you trust that amount of clearance? If you've done your sums right you should be able to. But would you?
I'd go for a bolt with the longest shank possible. Trouble is, bolts are made to standards (unless they're made in China). Threaded portion something like 2d+ 6mm ( can't remember). Either way, you're stuck with what's available or make a special.
Posted: Sun Oct 26, 2014 11:09 am
by Tapio
Corvus wrote:
It's a while since I was involved in this kind of thing, but my understanding is that the process involving zinc plating can induce hydrogen embrittlement. The process should be followed by passivation, if my memory serves correctly (Relying on memory is risky!)
http://en.m.wikipedia.org/wiki/Hydrogen_embrittlement
I agree with with Boxer dog. I've seen, first hand, examples of bolts fail easily under tension because of hydrogen embrittlement.
Edit: another associated link
http://www.heat.com.au/treatments-de-embrittle.php
I had no idea about this. I did know that you can get embrittlement if you use wet arc welding rods. They should always be stored in a heated cabinet.
If a screw is grade 8.8, then you know that tensile strength is 800 Mpa, (and yeld strength 800*.8=640 Mpa). You can take that info to the bank.
This is something to take into consideration when restoring an old bike or car. And another reason not to chrome parts
//T
Posted: Sun Oct 26, 2014 11:11 am
by 1200boxer
I'm worried about the stainless I can find here which is AISI 316,The breaking load is not far from mild steel.Maybe I could fit a non plated allen bolt and paint it?What I don't know is where to get one.
Posted: Sun Oct 26, 2014 12:04 pm
by Blackal
I would expect 316 SS to have at least 150% of the shear strength of mild-steel.
A good fact-sheet here:
http://www.google.co.uk/url?sa=t&rct=j& ... 0786,d.ZGU
Al
Posted: Sun Oct 26, 2014 12:20 pm
by 1200boxer